Fabricante de bebidas global expande capacidad y mejora consistencia
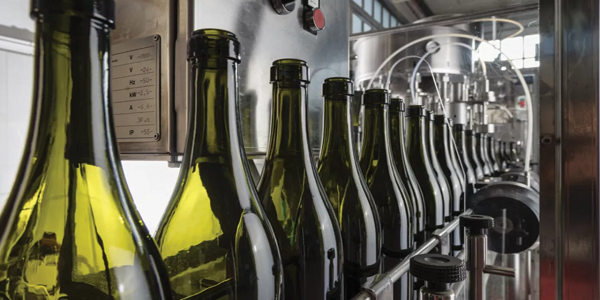
Contenido original: rockwellautomation.com/es
CASO PRÁCTICO | 5 minutos de lectura 🕛
📈 Desafío |
Expandir y migrar el sistema de lotes heredado a fin de mejorar el rendimiento y la consistencia del proceso de producción de bebidas. |
🛠️ Soluciones |
|
📉 Resultados |
|
Antecedentes
La consistencia y la seguridad del producto son fundamentales para cualquier proceso de fabricación de bebidas. Por décadas, los productores de bebidas han confiando en los sistemas de lotes no estandarizados a fin de mantener la calidad y el rendimiento del proceso.
Frente a las crecientes regulaciones, a la reducción del número de trabajadores calificados y la incesante demanda del mercado por una mayor variación de productos, los productores de bebidas requieren, más que nunca, una mayor estandarización.
Cuando un productor mundial de bebidas destiladas, cerveza y vino planificó expandir la capacidad de su planta en Illinois (Estados Unidos), recurrió a la empresa de diseño de procesos Barnum Mechanical, Inc. para una solución llave en mano. Barnum contrató a Industrial Automation Group para un nuevo sistema de control.
Con sede en Modesto (California, EE. UU.) Industrial Automation Group se especializa en soluciones de control de procesos para la industria de alimentos y bebidas. La empresa es un integrador de sistemas reconocido de Rockwell Automation y un miembro certificado de la Asociación de Integradores de Sistemas de Control (CSIA).
Desafío
“Mejorar la eficiencia del proceso de la base instalada era un objetivo fundamental para esta empresa de bebidas”, expresó NinivTamimi, gerente de Programas, Industrial Automation Group. “También planeaba incrementar su capacidad total al incorporar al sistema tanques intermedios, de dosificación, de embotellado y de almacenamiento de materia prima”.
La expansión de la planta fue considerable e incrementó las estaciones de camiones/vagones y los tanques de almacenamiento en un 75 por ciento aproximadamente en el área de recepción. La sala de mezcla experimentó un aumento similar. En embotellado, se agregaron tanques y algunos tanques existentes se convirtieron en “tanques versátiles”, que podrían utilizarse para el embotellado o el almacenamiento de materia prima.
“A medida que expandió su operación, la empresa planificó migrar a una solución de lotes 'todo en uno'”, explicó Tamimi. “Quería instalar un sistema eficiente que cumpliera con la norma S88”.
La norma ANSI/ISA-88 (S88) proporciona un conjunto coherente de terminología y estándares para el control de lotes en los sistemas de automatización industrial, incluidos el modelo físico, los procedimientos y la gestión de recetas. El sistema existente no cumplía con la norma S88.
“El software de la base de datos comercial se utilizaba para el almacenamiento de recetas, y el sistema de loteo completo se programó utilizando el código de Visual Basic for Application (VBA) y su HMI heredada”, expresó Tamimi. Para lograr una calidad del producto aceptable con el sistema existente, la planta a menudo necesitaba implementar dos o tres correcciones de lote por cada lote. El tiempo de prueba para la corrección de cada lote era de aproximadamente dos horas. Además, el sistema no contaba con capacidades redundantes ni de conmutación por fallo.
“Como resultado, si un servidor se caía, el sistema podía estar fuera de servicio entre dos y cuatro horas”, dijo Tamimi. “Además de mejorar la calidad del producto, nuestro cliente necesitaba incrementar la disponibilidad del sistema”.
Por último, pero no menos importante, la empresa requería de mejor seguridad. El sistema existente tenía solo tres credenciales: operador, supervisor y administrador. Las contraseñas para las credenciales se podían compartir fácilmente entre todos los usuarios. El cliente especificó que el nuevo sistema de procesos incorporara credenciales de conexión específicas del usuario, cierre de sesión automático y firmas electrónicas.
Solución
Industrial Automation Group implementó una solución de control basada en el sistema de automatización de procesos PlantPAx®, un sistema de control distribuido (DCS) moderno de Rockwell Automation.
“Con una solución PlantPAx, pudimos diseñar un sistema con alta disponibilidad que aprovecharía muchas tecnologías más nuevas, como la virtualización”, explicó Tamimi. “De hecho, elegimos un entorno virtual para esta aplicación”.
Rockwell Automation respalda la virtualización con el software VMware® Ready y recomienda el uso de la virtualización del servidor y VMware vSphere®, cuando se trata de aplicaciones de producción en tiempo de ejecución. La virtualización del servidor elimina la dependencia en un sistema operativo (SO) de computadora principal completo y suministra un entorno mucho más estable para las aplicaciones fundamentales.
El nuevo sistema incluye una plataforma de control multidisciplinaria, habilitada con información y escalable que combina el control discreto y de procesos con la comunicación y la E/S intrínsecamente seguras. El sistema completamente redundante controla las aplicaciones en las áreas de proceso como también las plataformas de limpieza en el lugar (CIP). El control remoto se integró para el procesamiento peligroso Clase 1, División 1. Se establecieron estaciones de trabajo de operador en la sala de control y las salas de loteo. También se colocó una estación de trabajo con ingeniería incorporada en la sala de control para la optimización en vivo del proceso.
Además, el sistema PlantPAx incluye las capacidades de visualización a nivel supervisión para brindarles una perspectiva óptima sobre la información del proceso. El software de gestión de datos, funcionamiento y visibilidad y gestión de la producción proporciona control de lotes y procesos.
Industrial Automation Group implementó el sistema en fases para mantener la planta en funcionamiento tanto como fuera posible durante la actualización. Primero se pusieron en línea las áreas de recepción de líquido a granel, incluidas las nuevas estaciones de camiones y ferroviarias como también los nuevos tanques de almacenamiento a granel. También se aplicaron a estos activos secuencias de limpieza en el lugar.
Luego, se agregó el nuevo sistema de loteo. Para implementar el sistema, se recrearon 120 recetas originales. Debido a la expansión de la planta y los nuevos activos en el sistema, se revisó el orden en que se agregaba el material como parte del proceso para disminuir el tiempo de lote y mantener la calidad.
“El control de calidad y las pruebas rigurosas fueron de suma importancia”, dijo Tamimi. “Antes de desmantelar el viejo sistema, tuvimos que demostrar que el nuevo sistema podía ejecutar las recetas existentes”. Una vez que la Prueba de aceptación de fábrica (FAT) se completó, el equipo integró el nuevo sistema de control durante una interrupción de dos semanas. Se realizaron más pruebas en el sistema, y los parámetros y las recetas se ajustaron según era necesario.
Resultados
“La planta ha mejorado la consistencia y el rendimiento general”, comentó Tamimi. “Además, la empresa puede agregar nuevas recetas más fácilmente con el sistema de lotes, ya que se comparten la mayoría de las operaciones y muchos procedimientos de unidad”.
Para optimizar aún más el desarrollo de recetas, el sistema permite una priorización dinámica basándose en la entrada del operador u otras variables definidas. Gracias a la funcionalidad del administrador de materiales dentro del software de lotes, no se necesita volver a escribir las recetas si el mismo material se encuentra en un tanque diferente.
Durante la fase de puesta en marcha, Industrial Automation Group ayudó a la empresa de bebidas a incorporar 50 recetas nuevas.
El sistema también mejora la generación de informes de la limpieza en el lugar. Realiza un seguimiento de todo el secuenciamiento y genera informes automáticamente, luego de que se completa cada ciclo de limpieza en el lugar, para documentar los procedimientos de limpieza adecuados antes de que se ejecute el siguiente lote.
Además, el sistema ayuda a asegurar la consistencia del producto.
“La materia prima no siempre ingresa al sistema con exactamente las mismas propiedades definidas en la receta”, explicó Tamimi. “Cuando ese es el caso, podemos actualizar los parámetros en el sistema y este ajustará de manera automática las cantidades de ingredientes para cada receta”.
Con el sistema PlantPAx, la planta de bebidas ha cumplido con su objetivo de no realizar más de una corrección de lote por lote.
Por último, el sistema ha ayudado a mejorar la seguridad con inicios de sesión individuales y firmas electrónicas. El sistema también impone un cierre de sesión automático de 15 minutos y exige que se vuelvan a ingresar las credenciales para todos los elementos fundamentales.
Contenido tomado de: rockwellautomation.com/es